Our Services
Concrete Joint Sealing
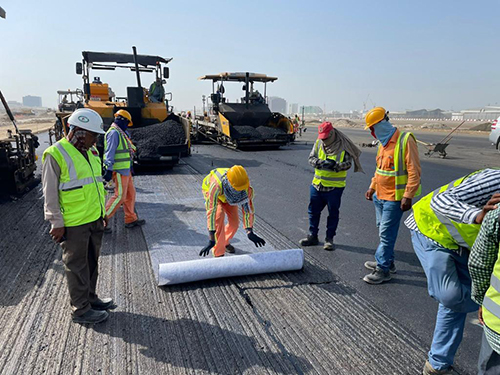
In the event of Crack sealing in asphalt after milling, Asphalt Geogrid is recommended after crack sealing (Fiberglass reinforcement with modified polymer coating and pressure-sensitive adhesive backing which bonding light Polypropylene nonwoven geotextile). For airfields flexible pavement projects Geogrid shall have Min. Tensile Strength of 100 KN/m & 200 KN/m for WARP & WEFT respectively.
Geogrid shall be installed after spraying Tack Coat and fixed using nails on corners. Before the New Asphalt overlay, another tack coat shall be sprayed over Geogrid. Asphalt geogrid will protect the sealant from flushing out during compaction.
More details at the following Method Statement:
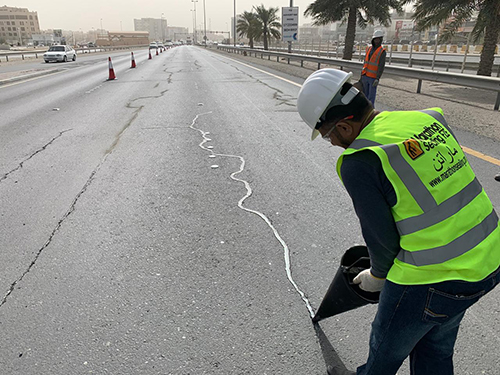
Crack Sealing and filling asphalt concrete pavement cracks is a common road maintenance
activity. Specialized materials are placed into or above cracks to prevent the intrusion of water
and incompressible material into the cracks and to reinforce the adjacent pavement. Crack Sealing & Filling delays the total reconstruction for several years and thereby saving cost.
More details:
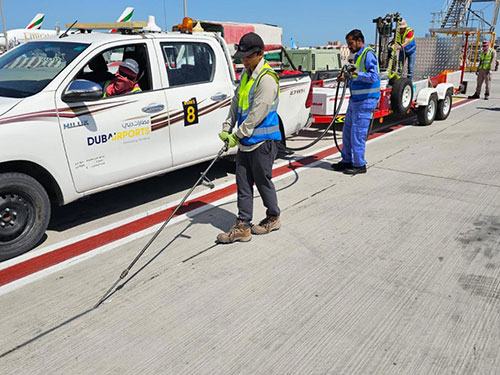
To replace the failed oil sealants at Concrete Joint Sealing, procedure shall be followed starting with cleaning of joint surface/substrate sound and homogeneous, free from oils, grease, dust, loose, or friable particles. The bond strength is directly dependent on the substrate condition, so it is essential that any weaker layer or cement laitance be removed to help bonding of the sealant directly to sound concrete. Weak, loose, or foreign material between the sealant and substrate will cause a failure point. The Concrete Joint Sealing surface should be
checked e.g. with a clean cloth on the surface, which should come away clean and free of dust or contaminants. It is important that this condition is achieved for the entire surface where the sealant will adhere, taking into consideration the sealant recess.
Complete details at Method Statement:
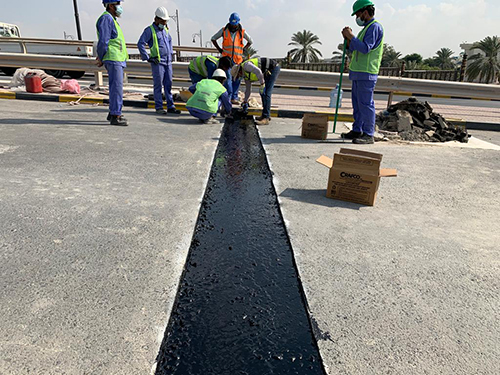
The Crafco Matrix 502 HD Joint can be used for both expansion and fixed end joints at abutments or piers in many bridge types including concrete slab, concrete beam, pre-stressed concrete and steel beam, either simple or multi-span, and / or under passes, in both new construction or rehabilitation projects. The joint is placed in the deck surfacing layer of either asphalt concrete or Portland cement concrete to a minimum depth of 2 inches (5cm).
Procedure described at below Method Statement:
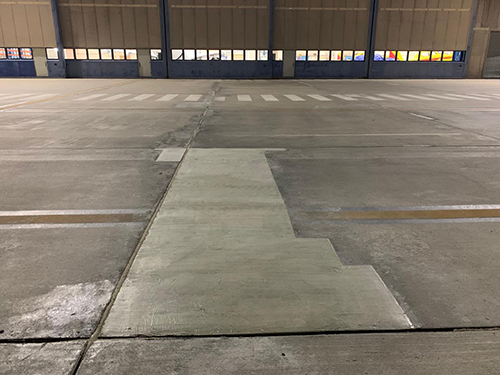
Repair areas at concrete slab to be prepared by light weight machinery such as cutters, planner, grinder, and jack hammer to facilitate proper adhesion, the pavement should be clean and dry and clear out of any dirt, dust or other contaminates. The material is then dispensed directly into the repair area through the chute from discharge valve at the rear of Patcher kettle then levelled with tools.
More details at below method statement
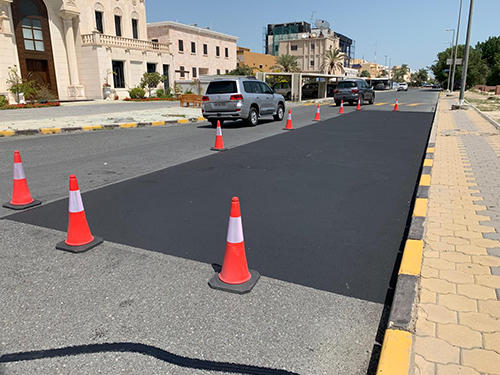
Sealcoating is the practice of applying a protective layer over asphalt pavements, such as airfields, taxiways, runways, streets, highways, community areas, service roads, driveways, and parking lots.
This coating, typically made from a mixture of water, sand, polymers, and other additives, protects the asphalt from oxidation, UV rays, and chemical spills. Regular sealcoating not only doubles the lifespan of the pavement but also enhances its appearance, providing a moisture-resistant, skid-free surface. Economically viable, sealcoating is a preventive maintenance option far less expensive than complete pavement replacement.
Application procedure can be found at below Method Statement: