Asphalt Crack Sealing
The effective preventive Asphalt Crack Sealing method for minimizing reflective cracking to the fresh asphalt wearing course and simply saving the new budget & investment.
We have seen many discussions among engineers and stake holders on effective methods to save the new wearing course, however the most effective ones have been selected as following steps after milling:
1- Crack sealing (Rout & Seal with Standard Reservoir and Flush)
2- Application of Geocomposite on top
3- Overlay of wearing course
In some cases, we have seen Geocomposite application has been cancelled due to various reasons such as site condition, design , and project management decision, and / or budget limitation. In any case, if only Geogrid application is being considered but cracking is detected which is not part of the base or underlaying layers’ failure, performance of crack sealing is highly recommended.
The basic fact behind the above can be easily seen at below illustration by Crafco Inc. which shows that cracking will always continue no matter what and sealing will help to minimize the extend of damages to upper and lower layers.
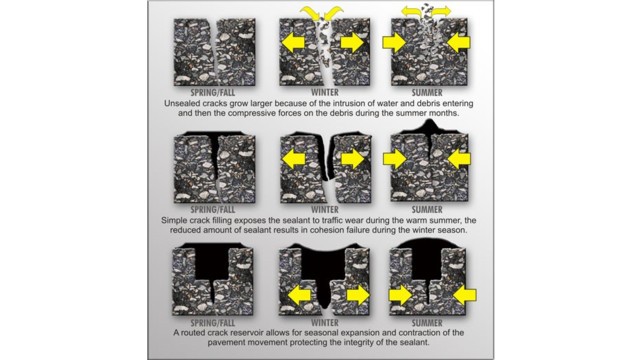
Cross section on Asphalt Crack movement
In this article we take a closer look at the asphalt crack sealing part and the best practice on steps to be taken in the application:
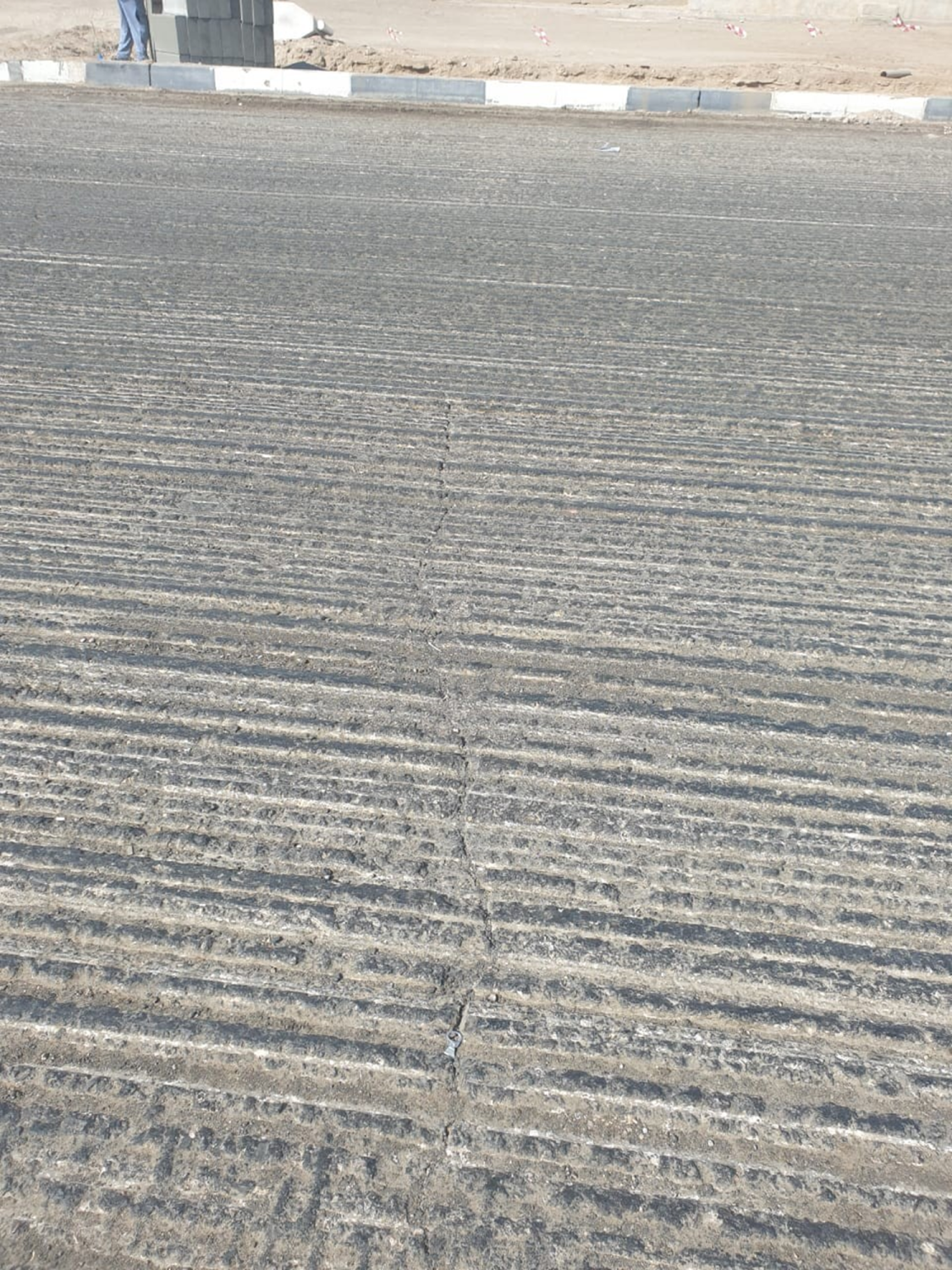
Sample of lateral cracking
Once cracking detected that is not part of the web cracking or structure failures such as sample pictures:
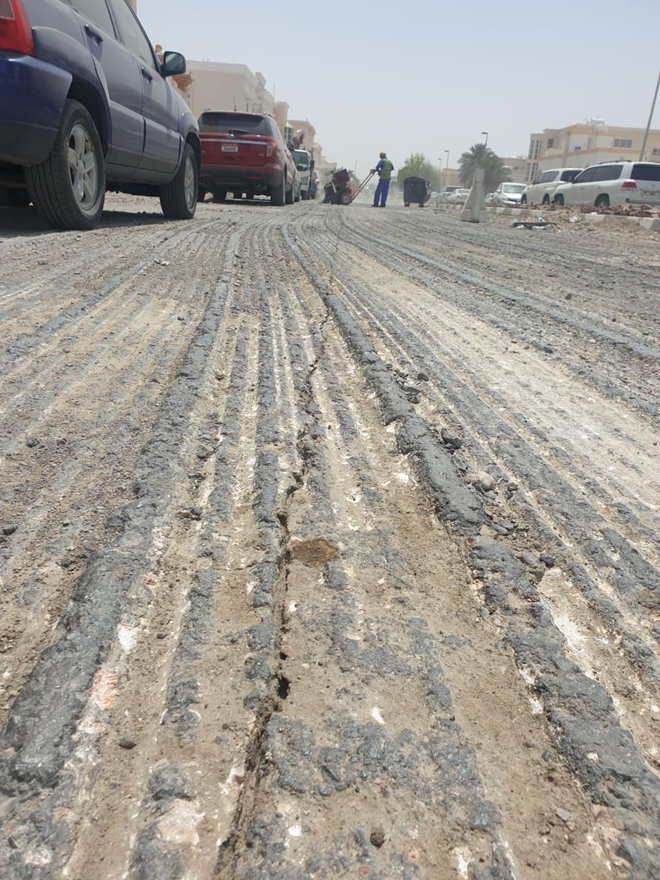
Longitudinal Cracking
The routing shall be done by a good quality asphalt crack router with the ability of chasing the cracks in a tough and hard old asphalt base to the nominal width of 20 mm.
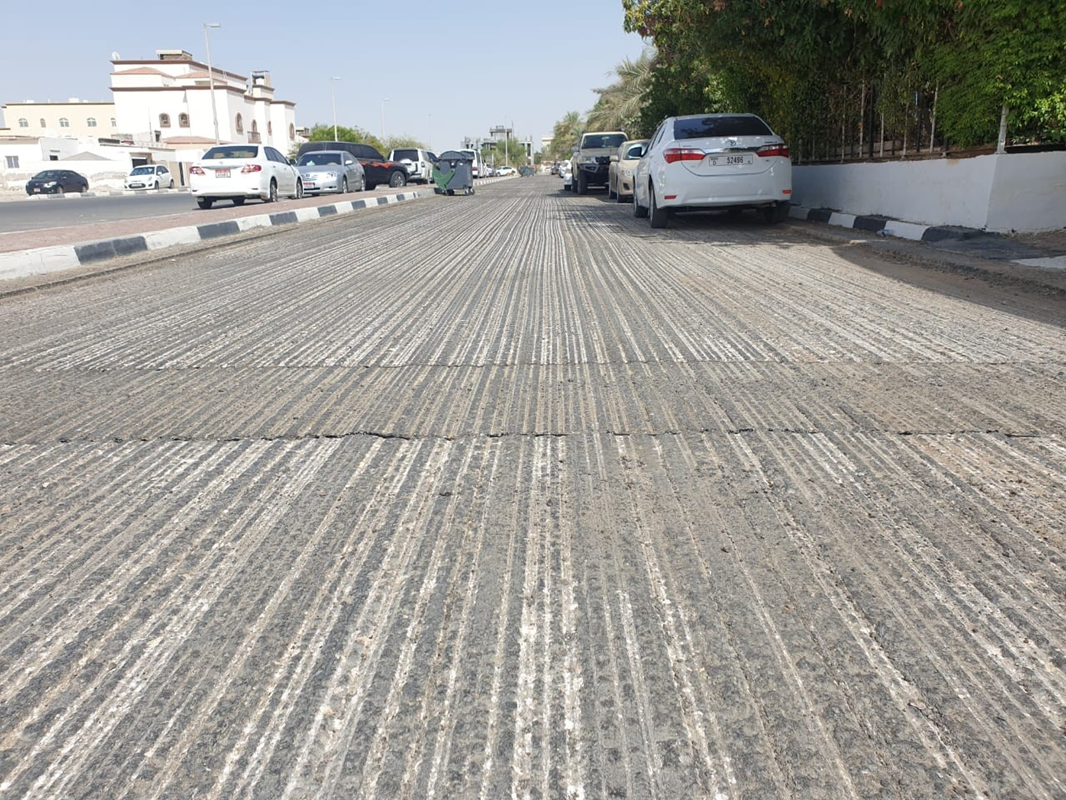
Sample of utility cutting cracking
The wider the crack, the more subject to pumping up the sealant to the new surface specially in hot weather condition.
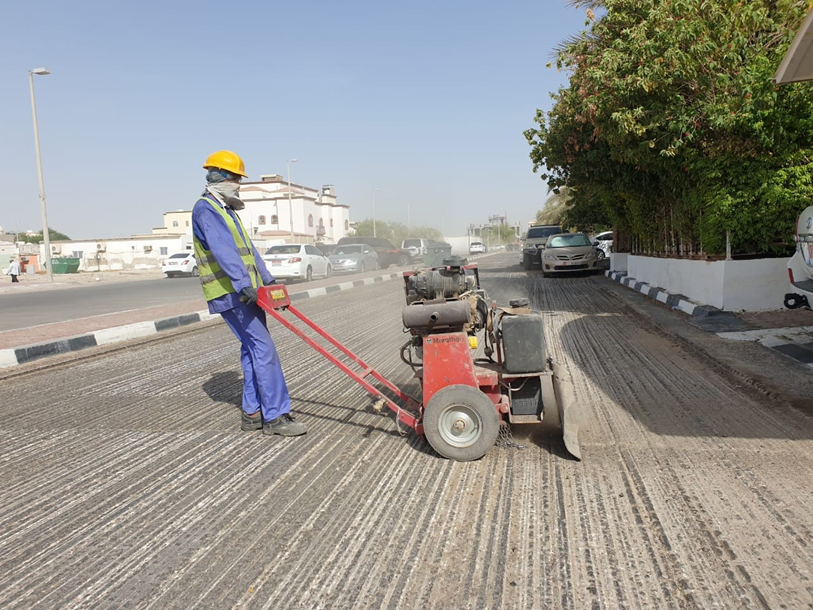
Asphalt Crack Router in action
The routing will help to remove the weak sides of asphalt crack sealing. Nominal depth varies between 10 to 20 mm.
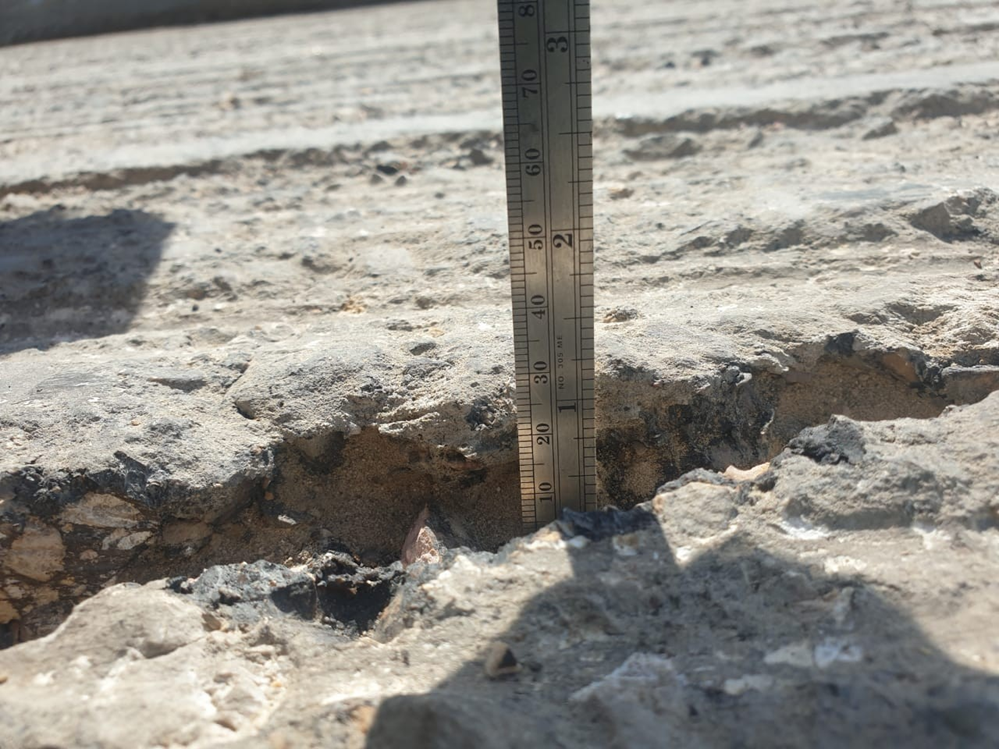
Routing Depth
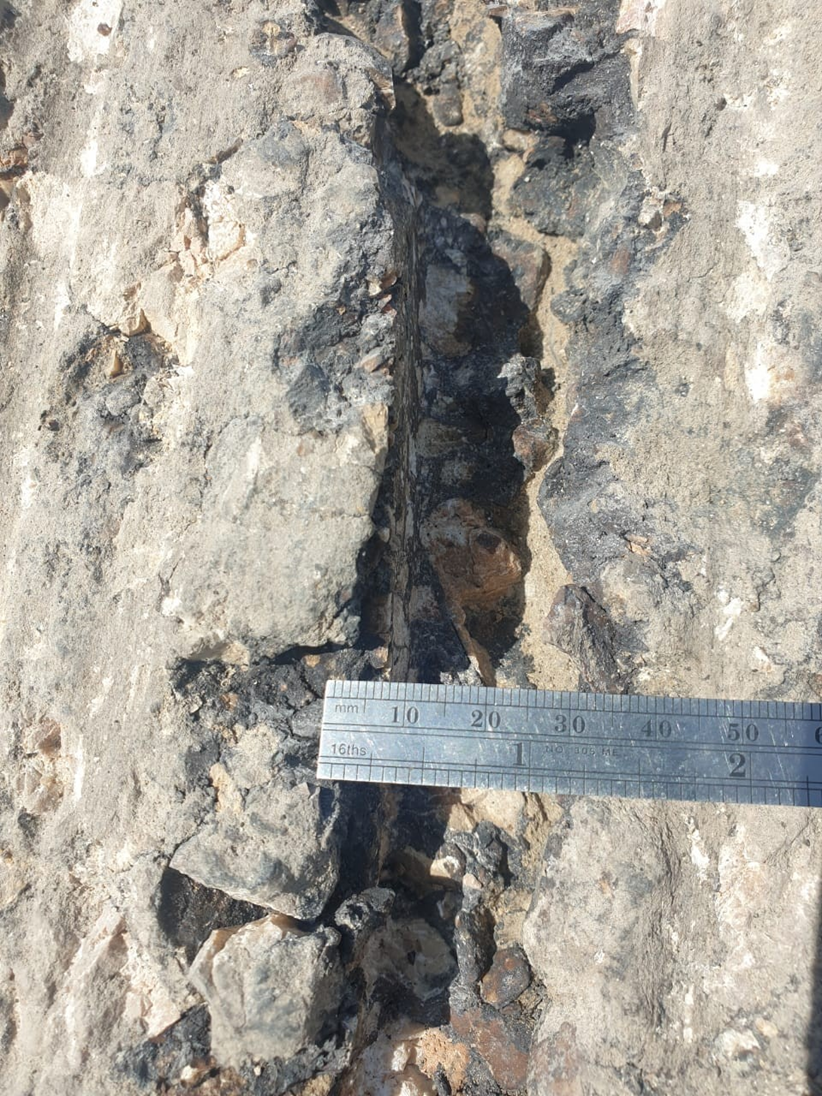
Routing Width
Router output would be approx. 100 LM of crack per hour in a suitable site condition.
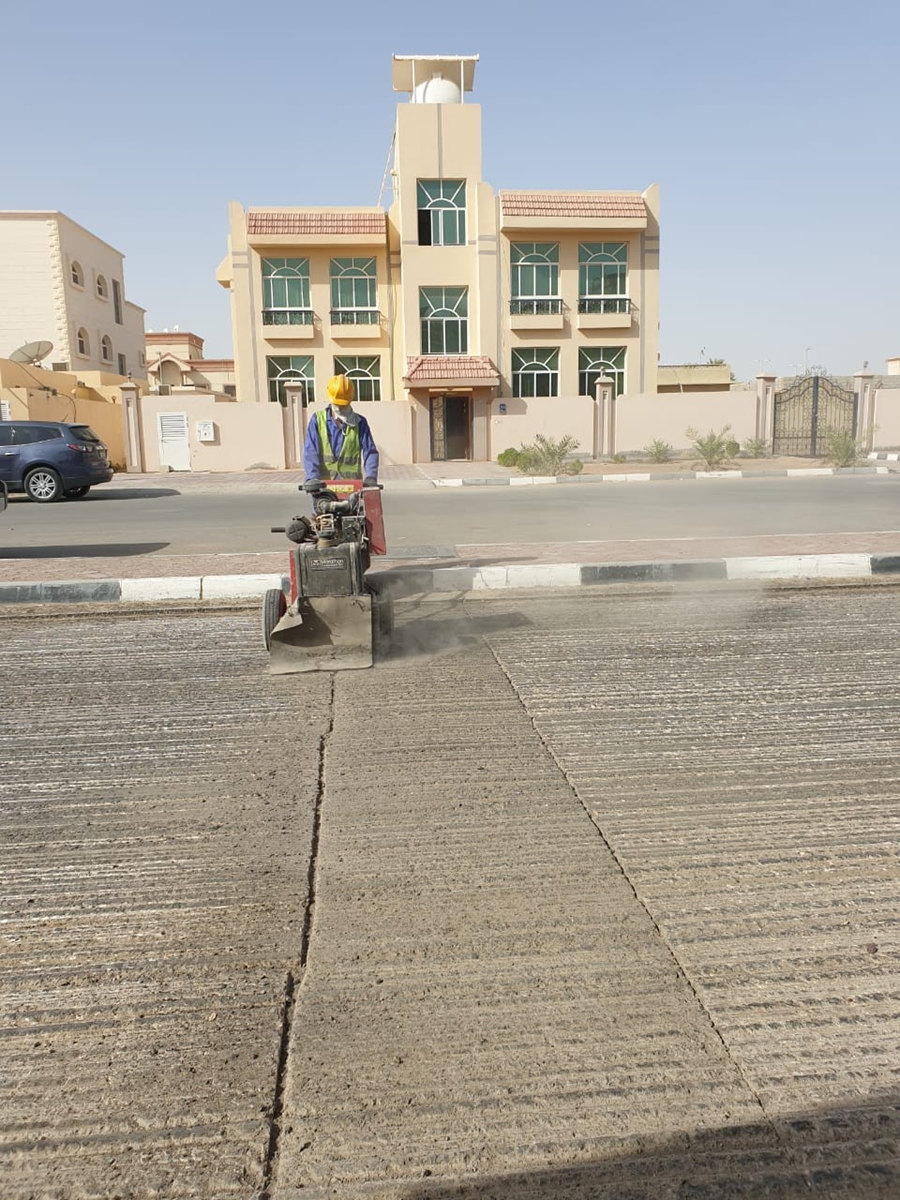
Creating reservoir
Cleaning is the critical part of the process and shall be done with patience and attention with compressed air.
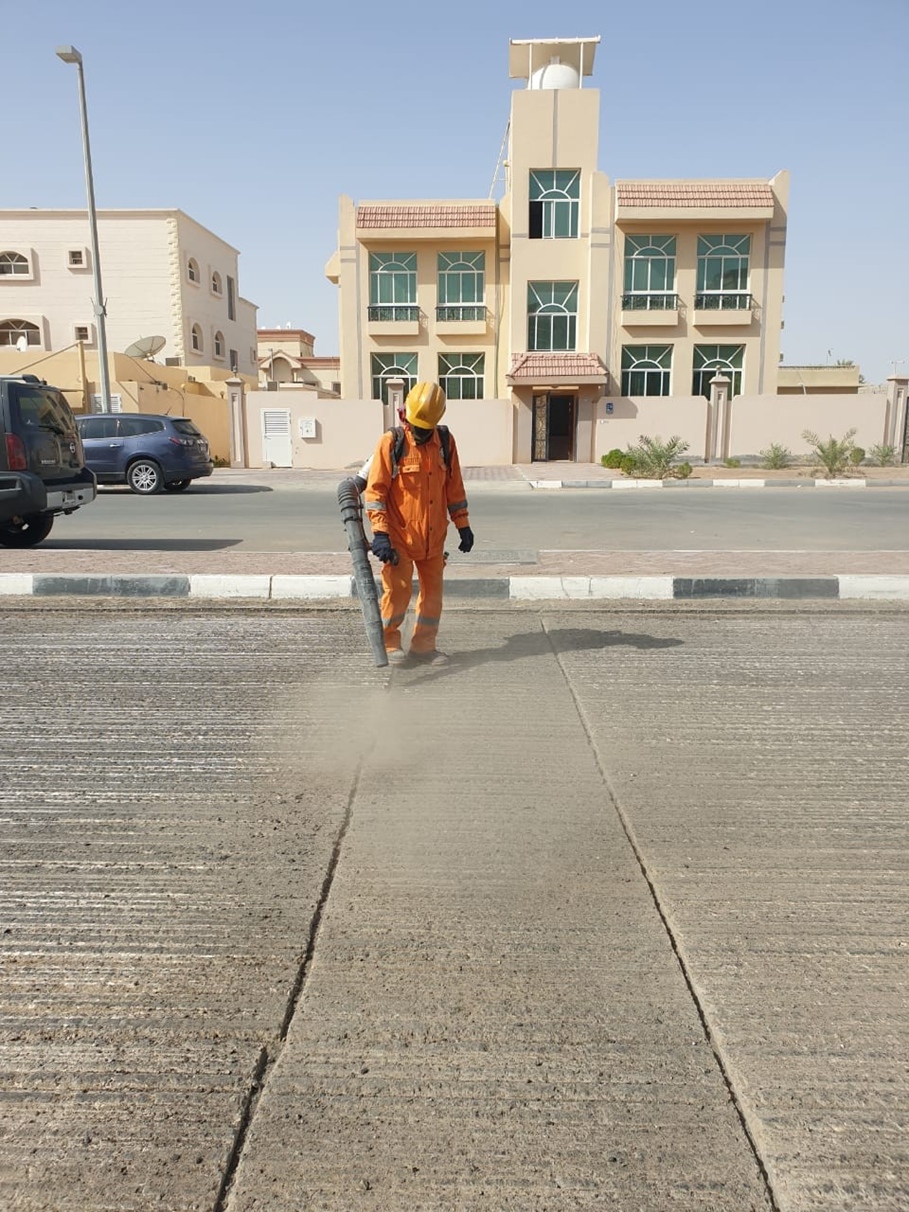
Surface and inside of the crack cleaning – Asphalt Crack Sealing
The rubberized hot applied sealant shall be applied to the #asphalt crack with 3 to 5 mm gap from the surface.
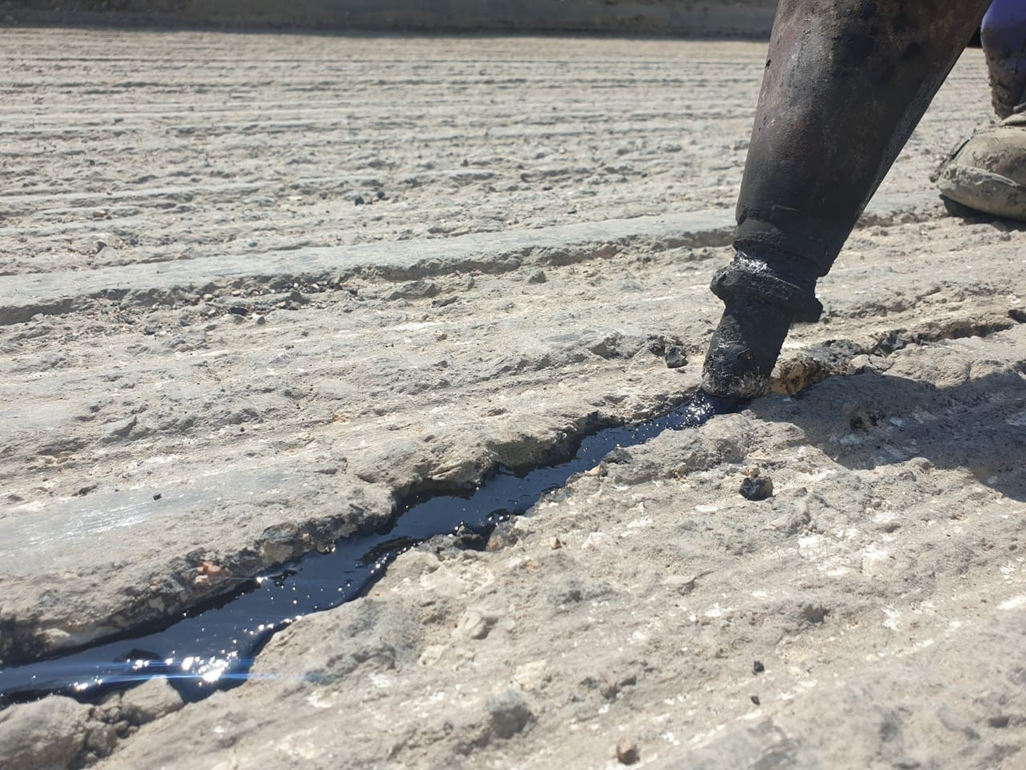
Hot Applied Sealant Injection at approx. 180 C
It is important not to overflow the reservoir to minimize the material surface touching the new asphalt.
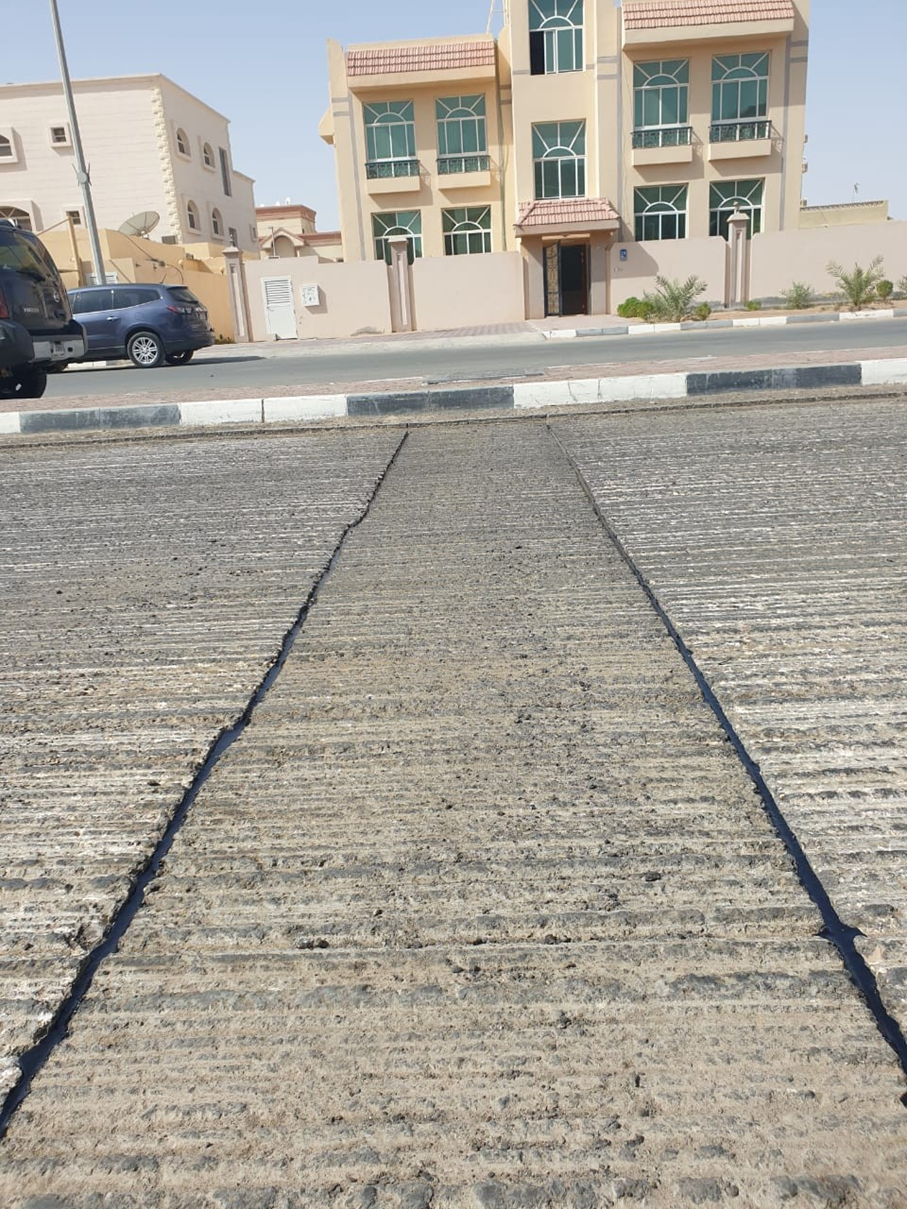
Sealed Crack
The space between the material and surface will help better curing and provides room for tack coat and new asphalt.
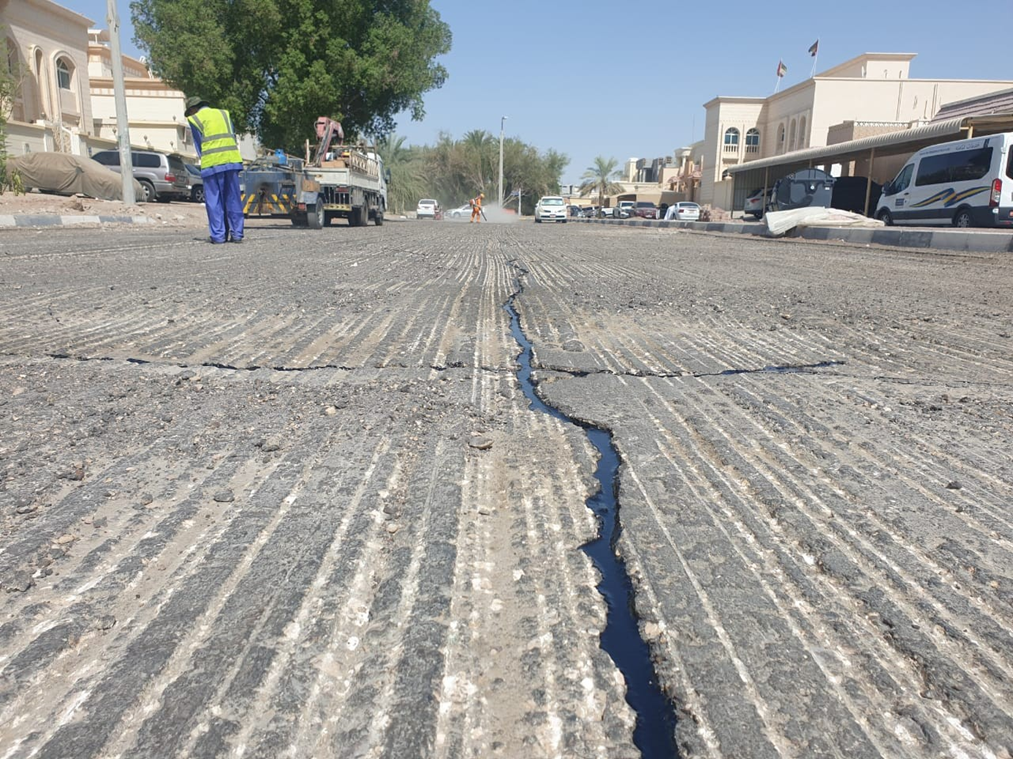
Sealed reservoir
Here are the temperatures involved in this process:
· Sealant application Temp. approx. 180 C
· Tack coat Temp. 60 C
· New asphalt overlay Temp. 140 C
If possible it is recommended to apply the new overlay at least 1 to 4 weeks after crack sealing to help out the sealant curing time.
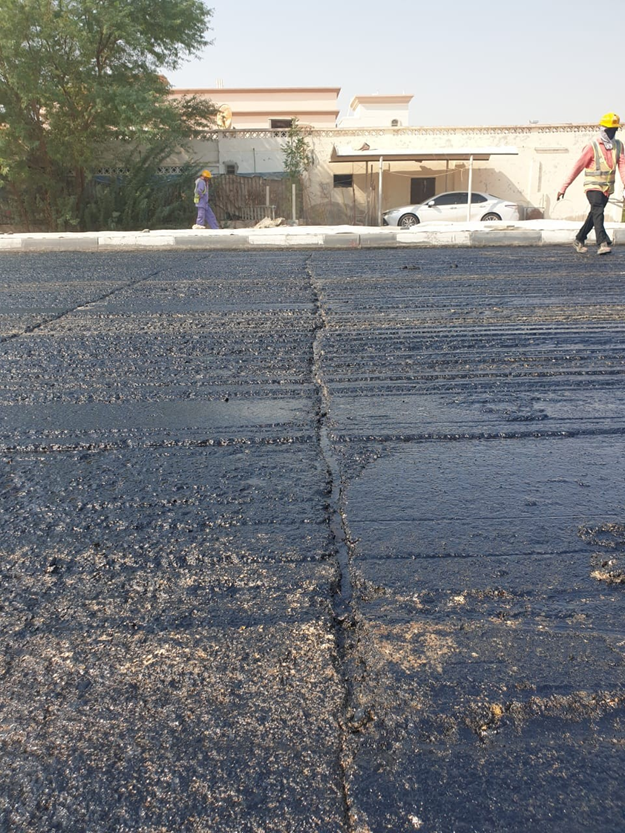
Sealed crack with sealant after tack coat
Types of the crack proper for this treatment are:
· Lateral and longitudinal
· Transverse cracking that occur roughly perpendicular to the centerline of the pavement. They can be caused by shrinkage of the asphalt layer or reflection from an existing crack. They are not load-related.
· Thermal cracking that may happen due to excessive temperature.
· Block cracking normally happens in rectangular pieces.
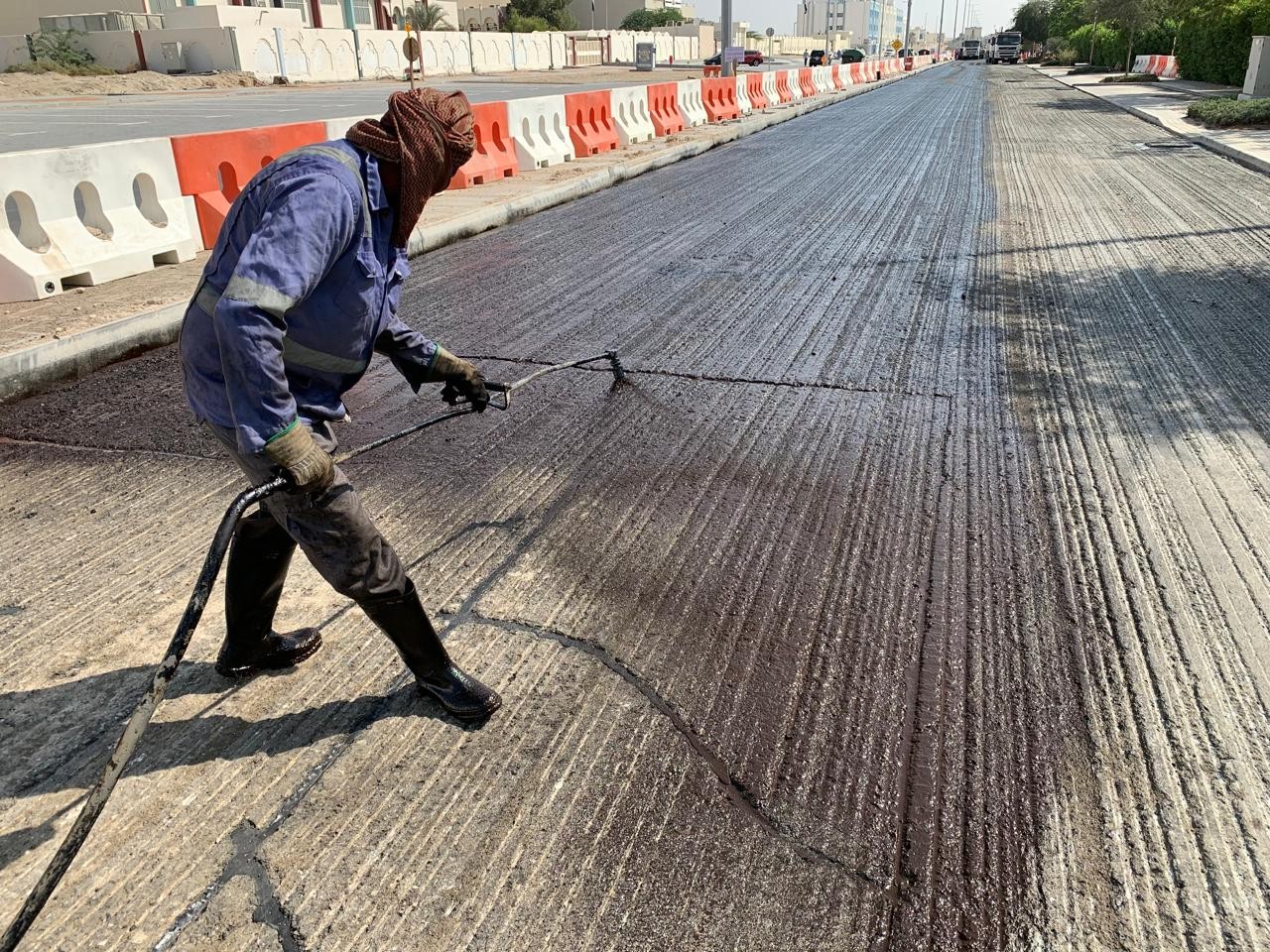
Tackcoat Application
The proper size of the crack for this treatment shall be from 4 mm to Max. 30 mm wide.
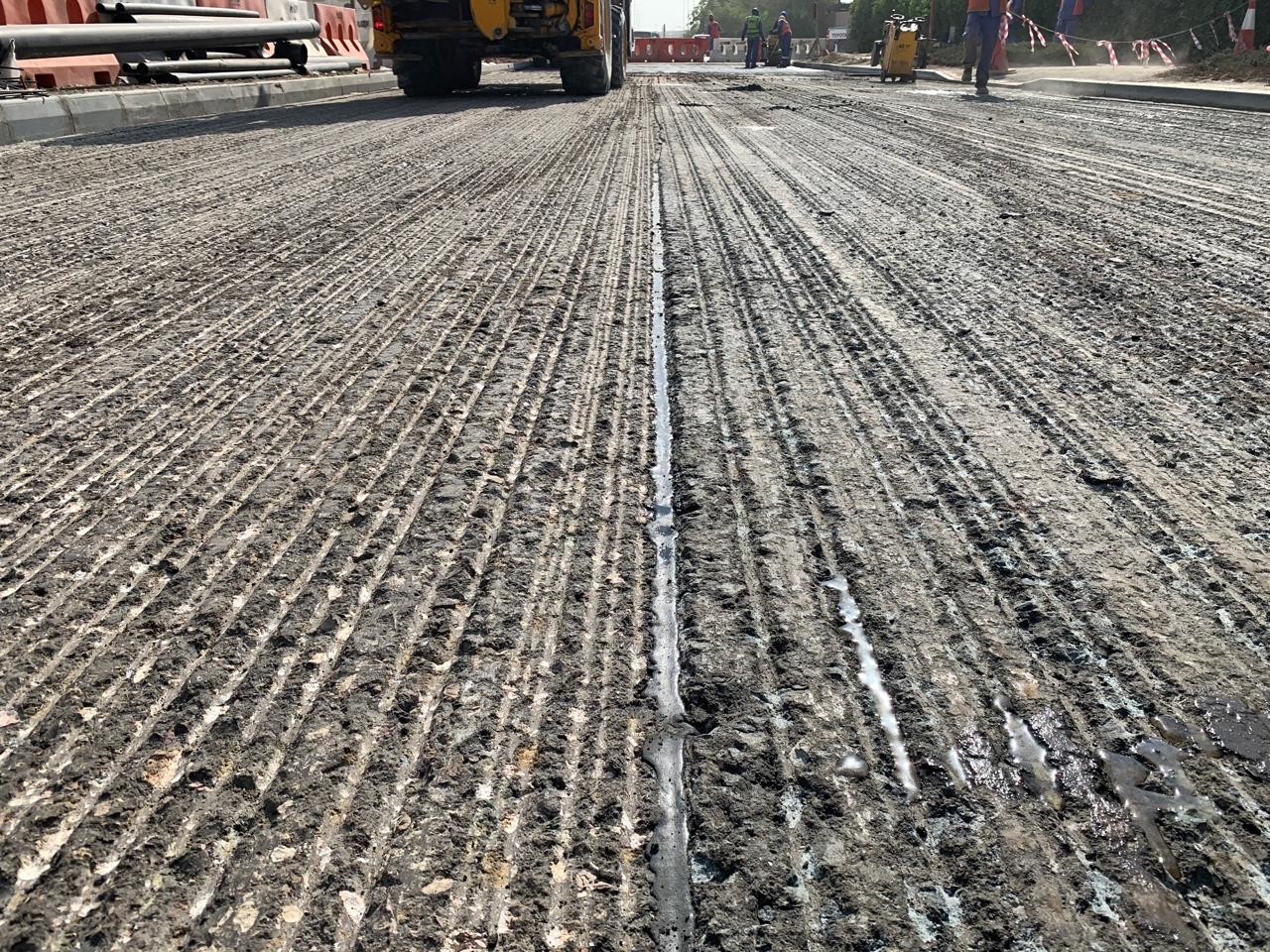
Sealed Crack
The sealant is supplied in solid form which when melted indirectly by oil and properly applied forms a highly adhesive and flexible compound that resists cracking in the winter and also resists flow and pick-up at summer temperatures.
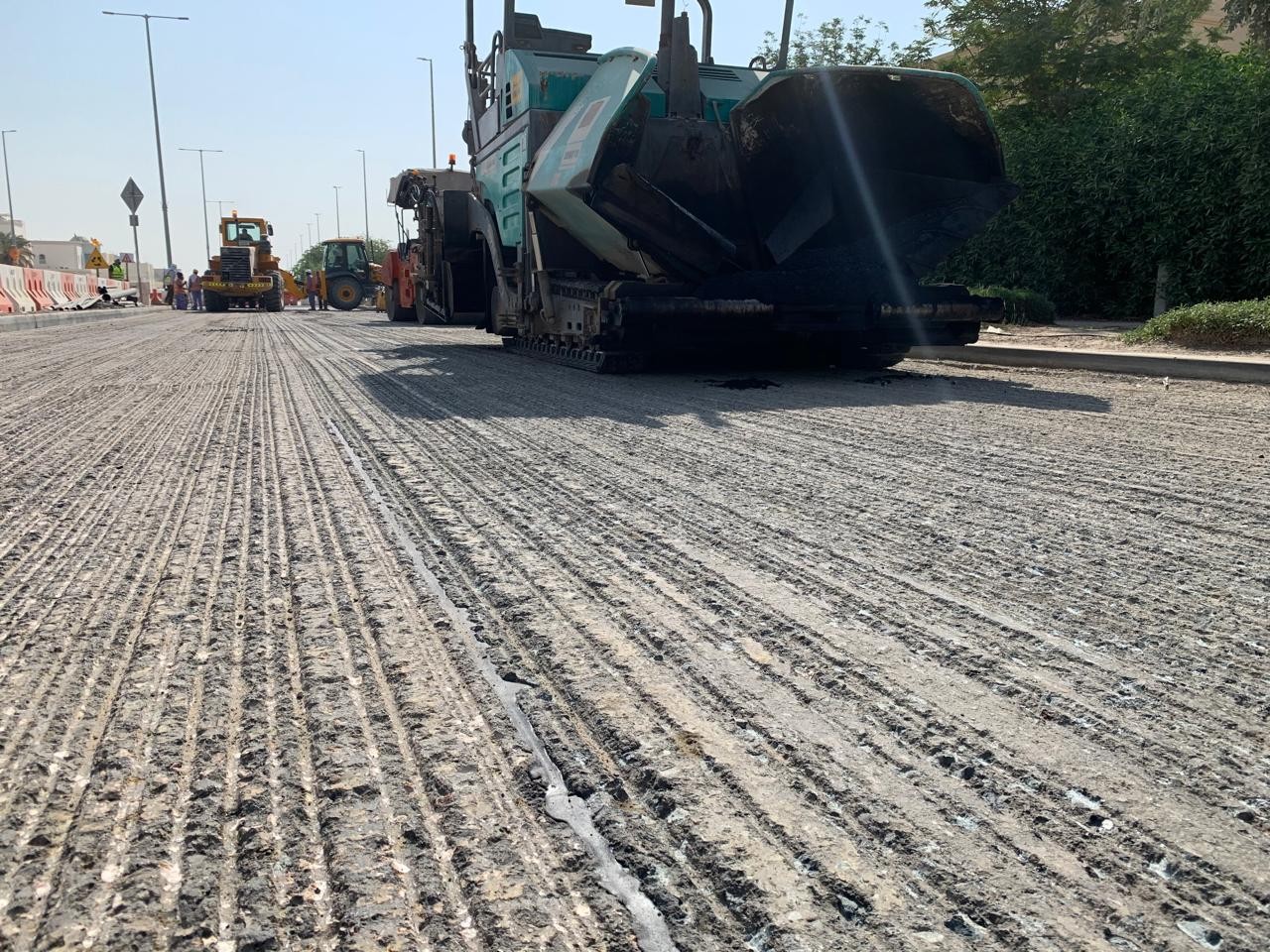
Sealant setting time varies from 15 to 30 min
The Geocomposite shall be cut in a manner to cover the sealed crack 37.5 cm from each side of the and in total width of 75 cm.
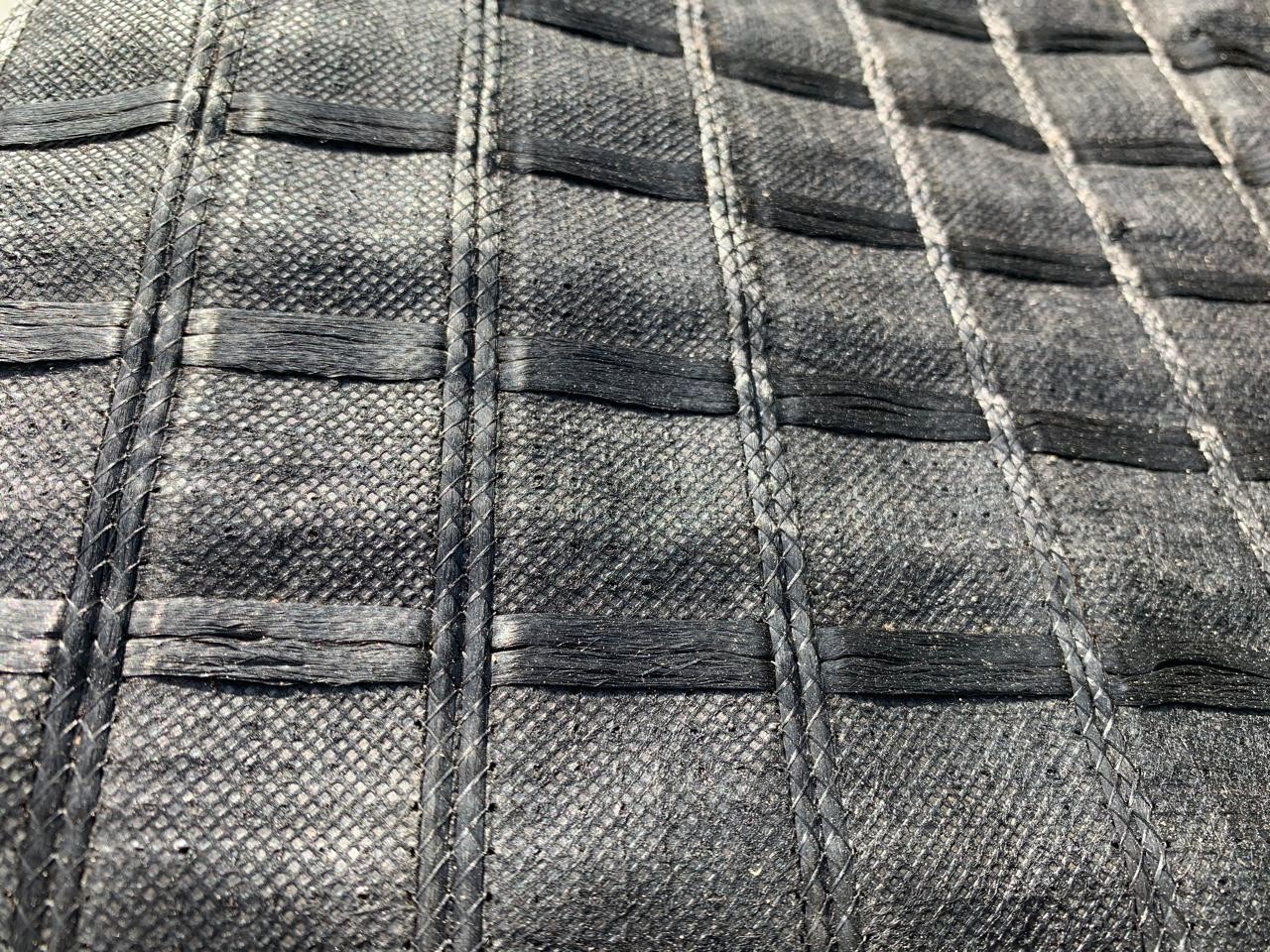
Geocomposite coating with MC
The material can also be nailed into asphalt to make sure it is not moving during the overlay oepration.
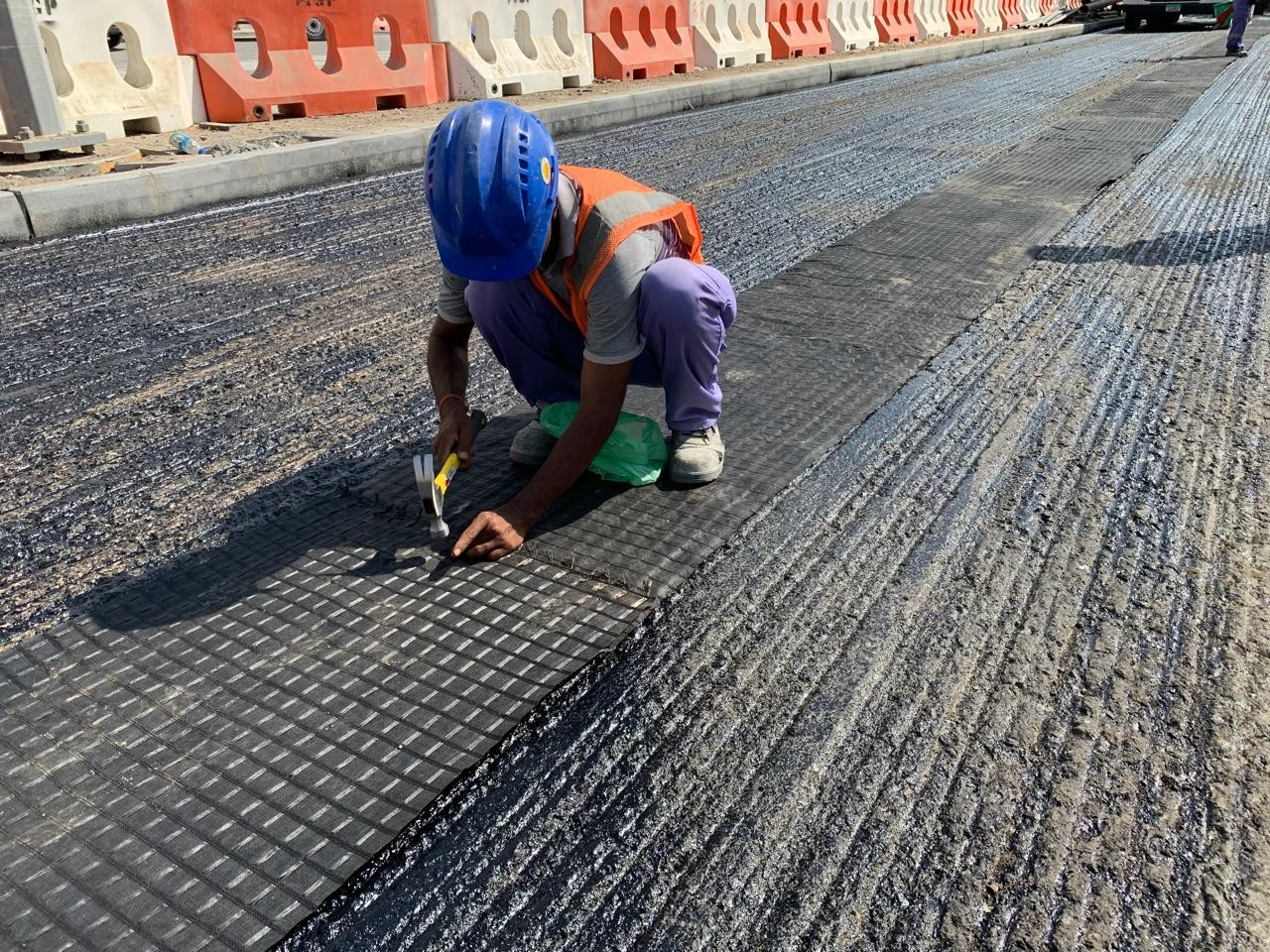
Nailing Geocomposite into milled asphalt after crack sealing and tack coat
The application of the grid depands on the damages exisiting after milling if some areas are having other distreeses spont larger width and lenght shall be considered.
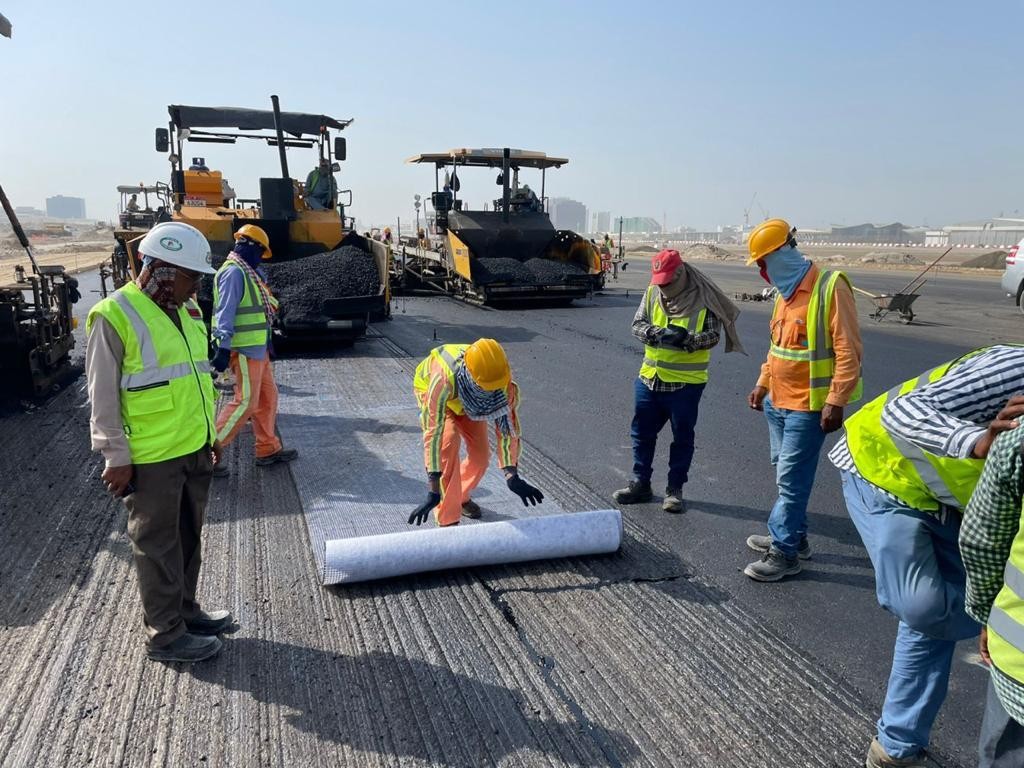
Geocomposite application
Having the geocomposite material protects the sealant from the heat of the new overlay and being intact to perferm its duty on preventing the reflection and more safeguarding the new overlay.
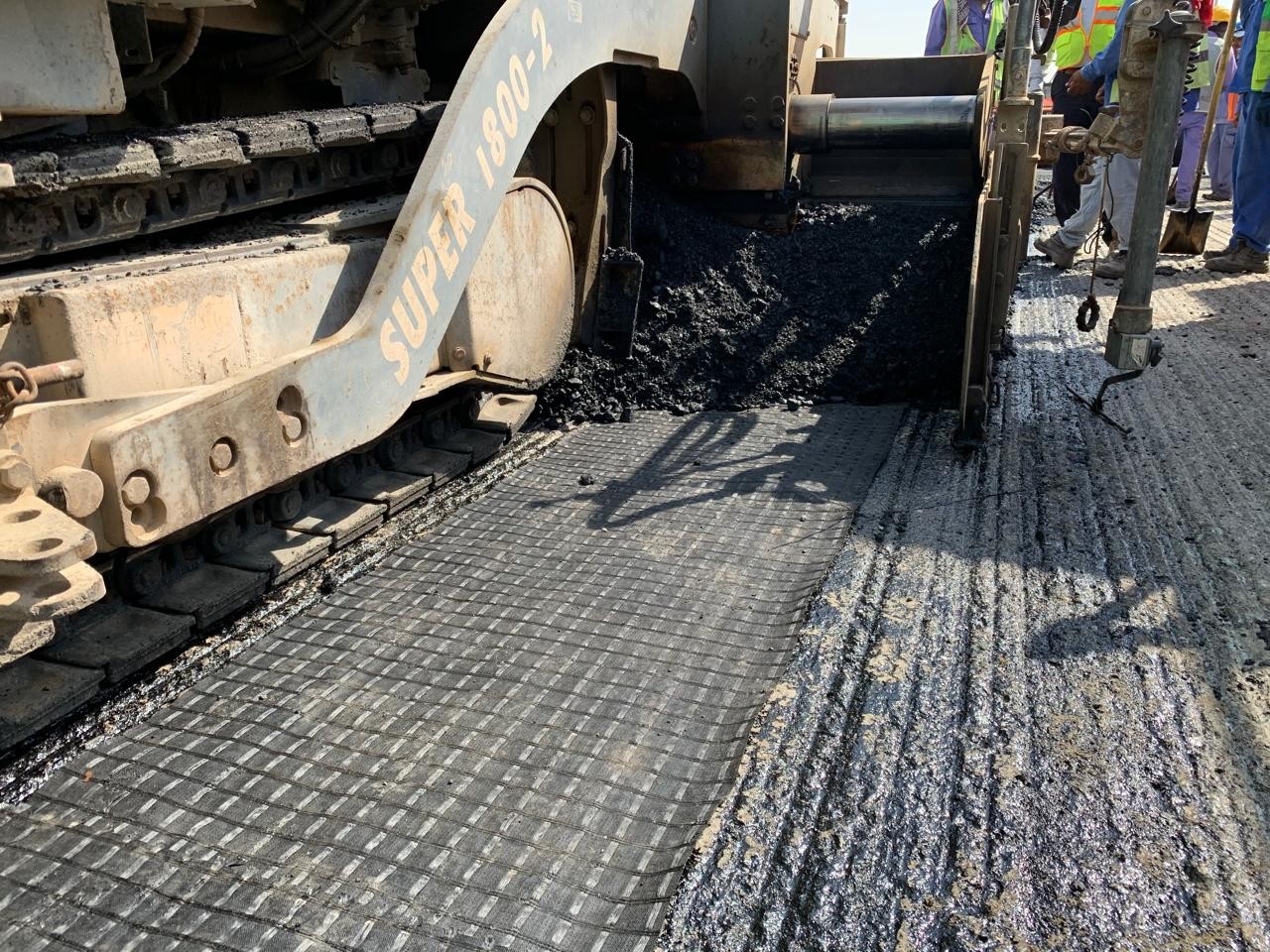
Overlay applicaion on top of Geocomposite
Copyright October 2024, www.marathonsealing.com